Pipe ramming cones are an intermediate component between the piercing machine and the pipe to be rammed. Their function is to transfer the impact energy generated by the mole/rammer to the pipe to be rammed. The size of the machine, and the resulting impact energy, determines the maximum size of pipe diameter that can be rammed with a particular piercing machine. The most popular MAX K130S can install steel pipes up to 323 mm in diameter. The MAX K180S can cope with ramming pipes with a diameter of 406 mm, and the rammer T240 can install pipes up to 711 mm in diameter.
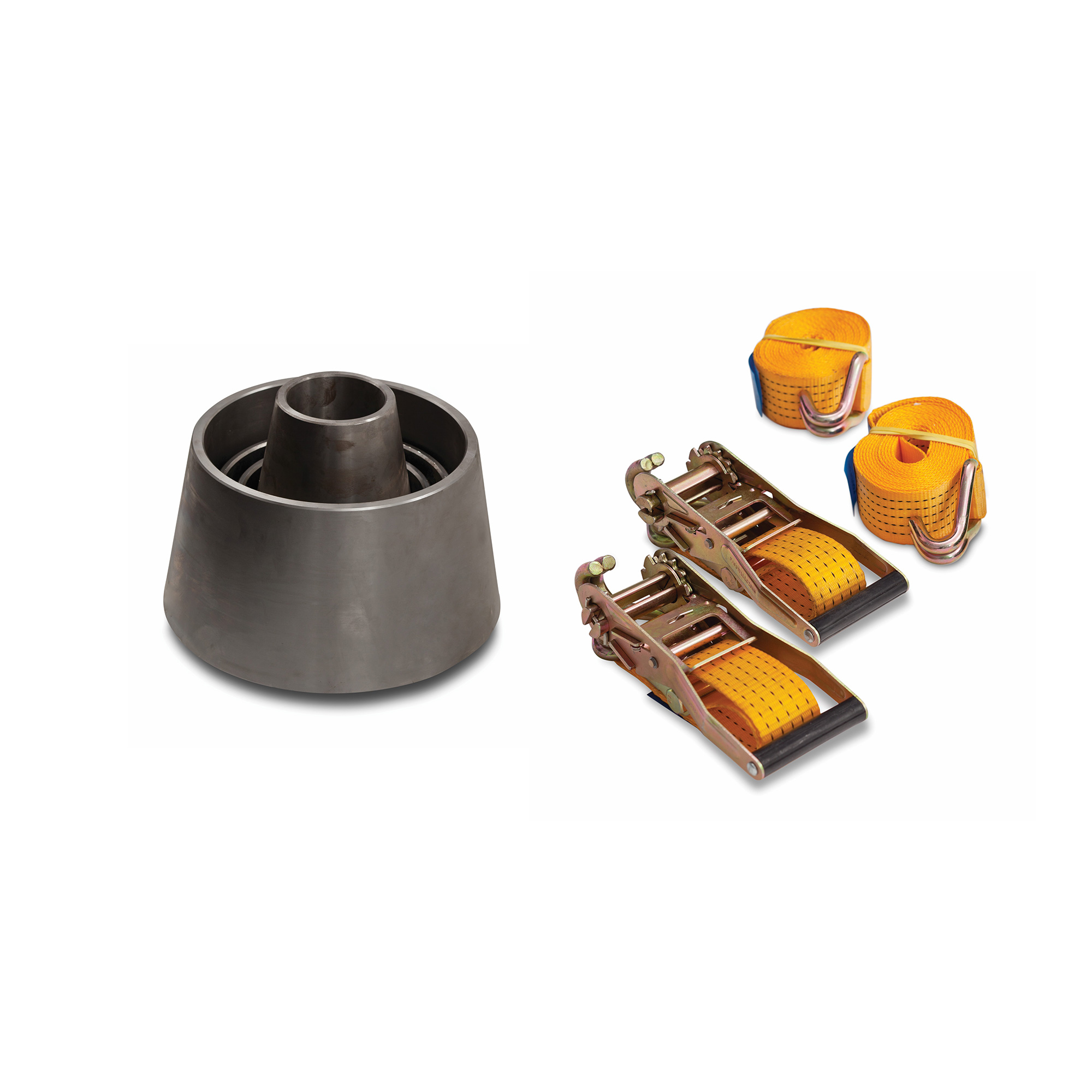
For each piercing machine, a cone, or set of cones, shall be mounted on the head of the mole, and then the entire machine shall be inserted into the end of the pipe to be rammed. In addition, it is necessary to weld on the end of the pipe ears made of steel rod, allowing to connect the pipe being rammed with the piercing machine by straps.
It is also worthwhile to armor the beginning of the pipe by welding on the outside of a ring made of steel rod, in order to increase the diameter of the hole made by the rammed pipe. As a result, the rammed-in pipe will have to overcome much less frictional resistance to the ground. In addition, it is also a good idea to weld a similar ring at the beginning of the rammed-in pipe in its interior. This will make it easier to remove the spoils from the rammed pipe later, using pipe plugs.
Which cone for which machine you need to use to install a certain diameter of pipe using a particular mole, is illustrated in the table below:
MACHINE |
CONE (mm) |
||||||
50-140 |
90-190 |
159-245 |
180-240 |
230-290 |
280-340 |
356-406 |
|
K95S |
SP for K95S |
STD for K95S |
- |
UNI |
- |
- |
- |
K130S |
- |
STD for K130S |
- |
UNI |
UNI |
UNI |
- |
K160S |
- |
- |
STD for K160S |
UNI |
UNI |
UNI |
UNI |
K180S |
- |
- |
STD for K180S |
UNI |
UNI |
UNI |
UNI |
This means that, for example, for the K130S piercing machine, for ramming a pipe with a diameter of 323 mm, it is necessary to have a 90/190 standard cone and additional cones of 180-240 mm, 230-290 mm and 280-340 mm. These cones are inserted one into another in a sequence, finally obtaining one cone which is the connection of the mole with the steel pipe to be rammed, as shown in the following schematic drawing.
In addition, as it can be seen from the table above these additional cones 180-240 mm, 230-290 mm and 280-340 mm, marked as UNI, can be used to ram pipes with other piercing machines: K160S and K180S. For these two moles, you only need to have the 159-245 standard cones dedicated to them.
To remove spoils from rammed pipe, pipe plug is used. It needs to be mounted on the end of the pipe securing it with locking rods. It is equipped with a foam pipeline pig which, adhering to the walls of the pipe, seals the whole assembly to ensure proper operation. A compressed air supply hose connects to the pipe plug. Pipe plugs are adjusted to standard steel pipe diameters.
You can find more information on how to do the work with different accessories here.