MAX Piercing Power trenchless technology tools belong to the category of pneumatic impact machines. Based on their application they can be divided into two main groups: moles and hammers. The easiest way to explain operation principles of such tools is to say that their construction is based on a reciprocating striker piston of high mass encased in a cylindrical housing made of high-tempered steel and powered by compressed air. The piston imparts its kinetic energy onto the head thereby moving the whole machine. The below animation shows the working principle of a pneumatic impact machine.
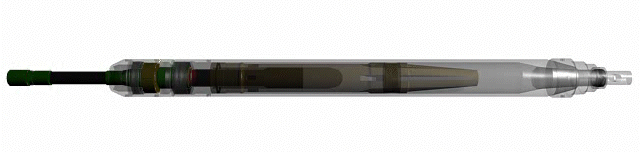
Compressed air is supplied to the mole through a supply hose. The air moves the piston encased in a cylinder (housing). The piston hits the element of the mole’s head called the anvil, and at the same time the air starts pushing the piston backwards, preparing it for the next forward stroke on the head.
The backward movement is based on a similar principle, the only difference being the position of driver elements in a mole, shifted through the pneumatic valve controlling the direction of work. After changing the position of the driver element, the air entering the mole pushes the piston in the opposite direction, so that it does not hit the anvil, but the back part of the device, where the tail screw is located.
Depending on the size of the machine, the piston hits the head 4-6 times per second. Based on this information it is easy to estimate how many such cycles (hits) occurs during the machine service life. We can assume that one stroke causes a 0.5 cm linear progress along the axis of the borehole (in practice it depends on soil conditions), which gives us 4000 strokes needed for a 20 m tunnel. Some of the companies using our products make up to 100 m of boreholes per day, which adds up to 20 km per year and is a result of 4 million piston strokes. And our tools have been used by some users even for up to 8 years.
It is worth mentioning that such impressive mileage is possible due to the use of Teflon guides and seals. These elements are worn in the first place, then they can be replaced at a very low cost, and after replacement the machine works for a long time like a new one, without air leaks or loss of efficiency. On the other hand moles without replaceable guides and seals require a scheduled overhaul after 5 km, as confirmed by one of their manufacturers*. The overhaul involves replacement of the used steel elements: the piston or/and the cylinder. This is a very expensive procedure, because these two components are the most important and the most expensive parts of the impact machine. Besides in machines without the Teflon seals the impact energy is gradually diminishing over the machine’s life cycle, due to increasing clearance between the piston and the housing.
The MAX series moles are capable of moving forward underground by means of displacing and compacting the soil, and equipped with the driver allowing remote pneumatic control over their work direction. They can be reversed during operation with a steering valve located on the control panel of the oiler – there is no need to stop the machine.
MAX rammers are tools for trenchless installation of steel pipes and other objects – with proper adapters. The standard set contains different diameter cones for inserting pipes. Some of the larger moles can be used for installing pipes as well, which makes them very versatile tools.
Pneumatic impact machines require a source of compressed air. We recommend the use of rotary screw compressors and the maximum working pressure of 7 atm.